By Shane Boyd, CHL, CRCST
When coming into the world of Sterile Processing from the OR, I was overwhelmed with all the processes. I had to spend time on the front lines with staff to see the workflows and barriers. With a filing cabinet full of count sheets, no access to digital copies, multiple binders of daily checks, and sterilizer load sheets in horrible handwriting, I was left scratching my head and thinking, “there has to be a better way.” We needed to improve our processes, make what we were doing more efficient, and stop errors caused by inaccurate count sheets. I started by making some small improvements. Then, it was time to find an instrument tracking system.
While going through the process of choosing a tracking system, I engaged three companies. I talked to multiple peers in the industry about each system. During these discussions, and speaking with the companies, I felt the most passion and commitment to the process from Ascendco. It was important to find a system that would partner with us and care about our success.
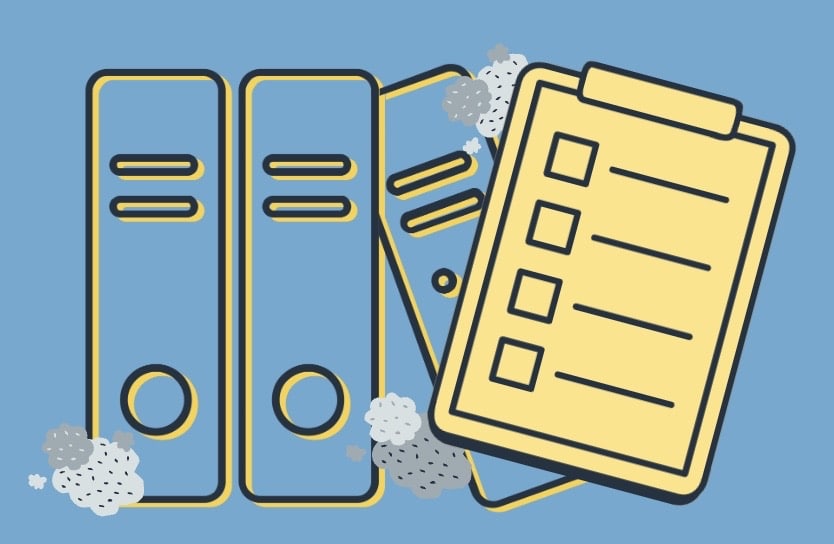
The next step was getting staff to buy into the idea of making the switch from paper count sheets to a tracking system. Gaining staff excitement for the system was not hard, I sought to make my passion their passion. However, anticipating a big change caused some anxiety. I knew my staff wanted to do the right things, but the daily grind of feeling overwhelmed and understaffed added stress to the idea of change. It was important to manage expectations, that a tracking system is not a magic pill that makes every departmental problem disappear. We would have to learn what it would do and what we would have to do to make it work. I believe that most people fear the unknown, even while being excited for it. Some staff wondered:
- “How will we do it?”
- “Will it actually make us better?”
- “Will it just be more work on top of the workload we have?”
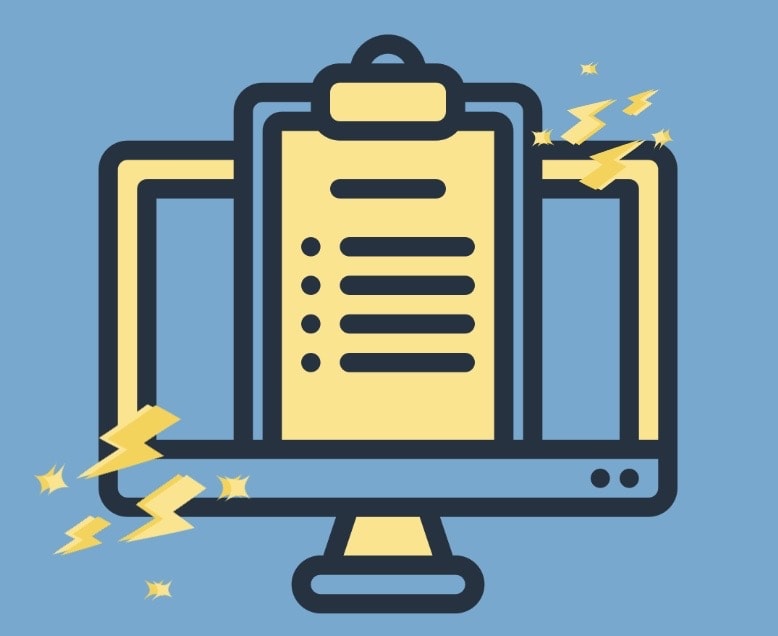
During go live, the training we received was essential. The Ascendco team was spectacular in helping us succeed. While learning the processes, the staff started seeing the benefits, like having the count sheet displayed with instrument data and pictures. We no longer had to commit all those details to memory. Additionally, the staff had visibility to sterilization parameters, special instructions, and integrated access to IFU’s on the assembly screen. The world of sterile processing is literally at our fingertips.
We have had the system for a little while and we’re continuing to improve the process by utilizing the its full capabilities. This has made it easier to track productivity, gain visibility to the location of instrument sets, and manage the maintenance and repair of the trays. Looking back, it’s hard to understand how we could do our work any other way. Most of the technicians are scheduled to test for their certification, and I believe it’s a reflection of trying to do the right thing and the passion they have felt from being empowered with a better way to do their work. The staff and I are really pleased and plan to keep enhancing our system and making improvements.